Capítulo 2 Fabricação de cloro e soda cáustica
2.1. Uma breve introdução sobre a indústria do cloro e da soda cáustica
O gás cloro (Cl2) e a soda cáustica ou simplesmente soda (NaOH) são produzidos exclusivamente por métodos eletrolíticos, usando cloretos fundidos ou soluções aquosas de cloretos de metais alcalinos. O processo eletrolítico é empregado em mais de 95% da produção mundial de cloro conforme dados informados pela Associação Brasileira da Indústria de Alcali, Cloro e Derivados, ABICLOR. A unidade de produção em plantas de cloro-soda é referida usualmente como ECU – “Electrochemical Unit” ou unidade eletroquímica. Na eletrólise da solução salina (conhecida como salmoura), hidrogênio, hidróxido de sódio ou hidróxido de potássio é produzido no cátodo e cloro gasoso é produzido no ânodo. Sendo que a energia elétrica é o item de custo mais importante devido ao fato das plantas de cloro-soda serem eletrointensivas. A posição do Brasil em relação a outras regiões do mundo pode ser observada na Tabela 2.1.
Tabela 2.1. Relação de empresas e tarifas de Energia Elétrica no ano de 1997.
Região / Empresa Valor (US$/MWh) | Valor (US$/MWh) |
---|---|
EUA – Costa do Golfo | 20 a 30 |
Oriente Médio | 10 a 20 |
Brasil - Trikem – (AL) | 32 (média) |
Brasil - Carbocloro – (SP) | 40 (média) |
Índia | 50 a 90 |
Sudeste Asiático | 60 a 70 |
Europa Ocidental | 25 a 50 |
A indústria de soda-cloro constitui uma das maiores tecnologias eletroquímica do mundo. Por ser um processo eletrointensivo, classificado como o segundo maior consumidor de eletricidade, com utilização anual de 2.400 bilhões de kWh, em 2006. Em 2010, a energia elétrica representou pouco mais de 45% do custo total de produção do setor. O consumo específico de energia elétrica por unidade eletrolítica é bastante significativo, e varia de acordo com a tecnologia de produção, se situando entre 2,8 MWh/t – 3,6 MWh/t. A Figura 2.1 ilustra o perfil evolutivo do consumo específico de energia (MWh por tonelada) pelo setor cloro-soda entre os anos de 2000 a 2010.
Recentemente, as empresas do setor promoveram expansões da capacidade instalada, aumentando em 10% a oferta de cloro no mercado brasileiro. Entre os anos de 2008 e 2009, ocorreu um aumento da produção com respeito à tecnologia de membrana, passando a apresentar o equivalente a 145 mil toneladas de cloro. Isto foi possível devido aos investimentos realizados pelas empresas Carbocloro S/A Indústrias Químicas e Solvay Indupa do Brasil. Em 2010, o setor fechou o ano com uma capacidade instalada de 1.536,3 toneladas de cloro. Sendo que a taxa média de utilização da capacidade instalada durante o ano de 2010 foi de 87%. A Tabela 2.2 ilustra algumas indústrias e sua capacidade instalada no ano de 2010 e a Figura 2.2 representa o percentual dos tipos de processos utilizada pelas indústrias.
O cloro e a soda cáustica desempenham um papel importante e significativo na fabricação de milhares de produtos dos quais nós dependemos no nosso dia a dia. A Figura 2.3 mostra um fluxograma representativo do processo envolvido na fabricação e consumo dos produtos obtidos durante a eletrólise da salmoura e a partir desses produtos (Cl2 e NaOH) é possível utilizar essa matéria-prima na produção de outros insumos em diversos segmentos da indústria.
Por exemplo, a soda cáustica é um produto essencial para operações industriais. Além de insumo importante na produção do alumínio, é utilizada na fabricação de papel e celulose, indústria química e petroquímica, sabões e detergentes, fibra sintética rayon, celofane, sais de sódio, corantes e pigmentos, vidros, produtos farmacêuticos, cosméticos, produção de hipoclorito de sódio e produtos para tratamento de água. É também usada na refinação de óleos vegetais, regeneração de resinas de troca iônica, na produção de tecidos de algodão para fortalecer as fibras e absorver melhor o tingimento, no processamento de metais, na extração de petróleo e na neutralização de efluentes.
Dados da Associação Brasileira da Indústria de Alcali, Cloro e Derivados mostram que a produção de cloro no Brasil registrou acréscimo de 1% no acumulado janeiro a dezembro de 2010, em comparação com o ano de 2009, somando 1.288.584 toneladas.
A fabricação de produtos derivados (uso cativo) do cloro foi de 88% no ano de 2010. O maior destaque foi para a produção de ácido clorídrico, que cresceu 5,7%, o DCE – material-prima para a fabricação do PVC, utilizado principalmente pela indústria da construção civil – com crescimento de 3,7% e o hipoclorito de sódio com aumento de 3,6%. O mercado interno apresentou um crescimento de 1,6% em 2010, o que corresponde a 12% do volume produzido
Tabela 2.2. Relação de indústria que produzem cloro e sua capacidade instalada no ano de 2010.
Cloro-capacidade instalada/2010 | Estado | Tipo de processo | Capacidade (t) |
---|---|---|---|
Carbocloro | SP | D | 147.900 |
Dow Brasil | BA | D | 415.000 |
Braskem | AL | D | 409.400 |
Aracruz | RS | M | 21.000 |
Canexus | ES | M | 47.753 |
Solvay Indupa | SP | M | 160.200 |
Braskem | BA | Hg | 70.300 |
Produquímica Igarassu | PE | Hg | 29.890 |
Carbocloro | SP | Hg | 107.100 |
Pan-Americana | RJ | Hg | 13.900 |
Fonte: Abiclor.
A produção de soda cáustica registrou um crescimento de 0,5% na produção em relação ao ano de 2009. Já o consumo aparente (produção local mais importações, descontado o volume exportado) apresentou alta de 8,8%. As importações de soda foram 19,7% maiores que o volume registrado em 2009. Em oposição ao observado no caso do cloro, aproximadamente 10% da sua produção foi utilizada pelas indústrias para produção de derivados (uso cativo). Sendo que os demais 90% foram vendidos no mercado interno para diversos segmentos industriais. Em 2010, ocorreu um aumento do consumo de soda cáustica em comparação ao ano de 2009 pelos setores químico/petroquímico e papel e celulose de 5,1% e 7,1%, respectivamente. Esses setores representam 22% e 25% do consumo de soda, respectivamente. A Figura 2.4 mostra a distribuição do consumo de soda cáustica em 2010 nos diferentes segmentos.
Em 1774, Karl Wilhelm Scheele descobriu a substância Cloro, Cl2. Esta substância é encontrada na temperatura ambiente no estado físico gasoso, sendo um gás extremamente tóxico e de odor irritante. Uma das suas característica interessante está no fato dele ser duas vezes e meia mais pesado do que o ar atmosférico.
2.2. Fabricação do cloro e da soda cáustica
Célula de Diafragma
A representação esquemática do processo de produção de cloro e soda cáustica através da eletrólise de uma solução salina é mostrada na Figura 2.5. A salmoura é introduzida na região do ânodo e os íons cloretos são oxidados a cloro por meio da passagem de corrente entre o cátodo e o ânodo. Os íons de sódio migram do ânodo para o cátodo através da membrana separadora. No cátodo ocorre a reação de redução do hidrogênio formando o gás hidrogênio e NaOH as reações são apresentadas a seguir:
Ânodo: 2Cl−(aq) → Cl2(g) + 2e−
equação 2.1Cátodo: 2H2O(l) + 2e− → 2OH−(aq) + H2(g)
equação 2.2Reação Global: NaCl(aq) + H2O(l) → NaOH(aq) + ½H2(g) + ½Cl2(g)
equação 2.3As cubas de diafragma produzem aproximadamente três quartos da soda cáustica nos Estados Unidos. Na operação de uma cuba de diafragma típica, o cloreto de sódio ou de potássio, quase saturados e a aproximadamente 60-70 ºC é admitido no compartimento anódico e passa, através de um diafragma para o compartimento catódico, onde se forma o álcali. O escoamento é continuamente mantido no diafragma na direção do cátodo, graças a uma diferença de pressão.
O processo de produção industrial consiste de:
- Unidade de tratamento da salmoura;
- Sala de eletrólise;
- Unidade de evaporação;
- Sistemas de processamento do gás (Cl2 e H2);
- Purificação da soda cáustica.
A Figura 2.6 mostra o fluxograma típico de uma indústria de produção de cloro e soda cáustica. A primeira parte do processo de fabricação do cloro e da soda cáustica utilizando célula de diafragma é a purificação da salmoura. Sendo eliminado inicialmente os íons cálcio, ferro e magnésio pela adição de carbonato de sódio e hidróxido de sódio a solução de NaCl. Esse procedimento é útil, pois diminui o entupimento do diafragma, o que poderia elevar a tensão da célula e, além disso, a adição de NaOH favorece a obtenção de uma soda cáustica mais pura. Por causa da adição da base é preciso neutralizar a solução utilizando em geral ácido clorídrico. A salmoura então é transferida para as células eletrolíticas para que possa ocorrer a eletrólise. Cada célula eletrolítica usa de 3,0 a 4,5 V, por isso, são ligadas em série, para aumentar a voltagem de cada grupo.
O processo de eletrólise apresenta em média uma eficiência da ordem de 50%, por isso, a solução de NaOH está contaminada com NaCl, para recuperar o cloreto de sódio que não foi processado durante a eletrólise, a solução de NaOH com concentração entre 10-12% é concentrada em um sistema de evaporação em estágios múltiplos. Esse sistema esta acoplado a um separador de sal e a um sedimentador, então após passar pelo sedimentador o sal é levado a um filtro lavador. O sal é separado da solução de soda cáustica devido a sua baixa solubilidade em solução de NaOH a 50%, a qual é de 1% de NaCl em NaOH. Finalmente, o sal recuperado pode ser reutilizado na preparação de uma nova solução de NaCl no início do processo.
A soda cáustica a 50% concentrada que sai do sistema de evaporação em estágios múltiplos e separador pode ser concentrada a 70-75% em outro evaporador de estágio simples, usando pressões da ordem de 5,0 – 7,0 atm. Mas, durante essa etapa o sistema precisa de tubulação com camisa de vapor, pois pode ocorrer solidificação da solução dentro da tubulação. Posteriormente, a soda cáustica pode seguir para tanques de sedimentação ou o sistema de produção de escamas, ou seja, as escamadeiras.
No outro lado, o cloro que sai da parte superior da célula eletrolítica esta arrastando com ele vapor de água. Para retirar a água do gás cloro primeiramente, o gás é resfriado o que favorece a condensação da maior parte do vapor de água, contudo, ele ainda apresenta uma quantidade muito grande de água, para deixá-lo seco é preciso passar o cloro em um sistema de torre que contem ácido sulfúrico, um agente desidratante, que vai retirar toda a umidade do gás cloro.
O cloro úmido não deve ser operado em tubulação feita em ferro ou aço, pois ele pode atacar esses metais. Por isso, nessa fase do processo o ideal é trabalhar com materiais mais resistentes, tais como: poliéster ou PVC (cloreto de polivinilo).
Célula de Mercúrio
A Figura 2.7 ilustra uma célula de mercúrio, em geral a célula é feita em aço na sua parte inferior com lados de borracha revestidas em aço. A célula apresenta 5 pontos de entrada e saída de reagentes e produtos os quais são: saída e entrada da solução de salmoura; entrada de mercúrio e a saída de amalgama de Hg—Na, e saída do gás cloro produzido no ânodo. Os eletrodos na parte superior da célula são chamados ânodos e são ajustáveis e mercúrio (que forma o cátodo da célula) flui na parte inferior com um ângulo de inclinação. A corrente flui a partir do fundo de aço para o mercúrio.
A salmoura (NaCl + H2O) entra na extremidade superior e entra em contado com o ânodo, o qual pela aplicação de uma diferença de potencial, eletrolisa os íons cloretos produzindo o gás cloro, que flui a partir da porção superior da calha e então sai. Os íons de sódio presentes em solução migram para o cátodo e reagem com o mercúrio para formar amálgama de sódio (uma liga de mercúrio e de sódio), que flui para fora da célula pela extremidade inferior dentro de um tanque cilíndrico vertical. Entre 0,25% a 0,5% de amálgama de sódio é produzida na célula. As seguintes reações químicas para o processo são:
a. Reações químicas que ocorrem no ânodo:
2Cl−(aq) → Cl2(aq) + 2e−
equação 2.4Cl2(aq) → Cl2(g)
equação 2.5b. Reações químicas que ocorrem no cátodo:
2Na+(aq) + Hg + 2e− → 2Na(Hg)
equação 2.6A reação química global para o processo é:
2NaCl(aq) + Hg → Cl2(g) + 2Na(Hg)
equação 2.7Por sua vez, a amálgama de sódio-mercúrio que sai da primeira célula eletrolítica entra em uma segunda célula eletrolítica (célula secundária) onde agora a amálgama se torna o ânodo e o outro eletrodo (cátodo) em geral é feito em aço (ou ferro) ou grafita. Para que a reação de formação de hidróxido de sódio ocorra é injeta em contracorrente água purificada. O gás hidrogênio formado no cátodo, saturado com vapor de água, sai pela parte superior, juntamente com os vapores de mercúrio. A soda cáustica então flui para fora da célula com uma concentração entre 40-50%. Para se aumentar a concentração do NaOH é preciso aumentar a temperatura de operação da segunda célula, em temperaturas acima de 100 ºC é possível obter uma solução de hidróxido de sódio com concentração entre 70-75%.
Algumas células são concebidas com saída de cloro e escoamento de anólito a partir da caixa final, que são separadas no tanque de salmoura esgotada. O mercúrio, a partir da decomposição, é bombeado de volta para a primeira célula. A seguir são apresentadas as reações para a segunda célula:
a. Reação química anódica:
2Na(Hg) → 2Na+(aq) + Hg + 2e−
equação 2.8b. Reação química catódica:
2H2O(l) + 2e− → 2OH−(aq) + H2(g)
equação 2.9Reação química global do processo:
2Na(Hg) + 2H2O(l) → 2NaOH(aq) + Hg + H2(g)
equação 2.10O gás de hidrogênio que é formado a partir das células de cloro-álcali é normalmente utilizado para a produção de ácido clorídrico ou utilizado como combustível para produzir vapor. No caso do hidrogênio, produzido pelas células de mercúrio, o mesmo precisa primeiramente ser purificado através do processo de congelamento (resfriamento), porque apresenta contaminação por mercúrio. Durante o resfriamento o mercúrio é separado do gás e, então pode ser devolvido para a primeira célula eletrolítica. Esse processo não é suficiente para remover todo o mercúrio presente no gás, assim, em geral, o hidrogênio passa por um tratamento secundário para remover traços de mercúrio que ainda persistem. Esse tratamento consiste em passar o hidrogênio em uma coluna contendo uma peneira molecular. Finalmente, o gás hidrogênio é comprimido em cilindro.
Em casos especiais, em virtude da solicitação de hidrogênio quase puro contendo pequenas quantidades de oxigênio, algumas plantas podem aquecer o hidrogênio sobre um catalisador de platina (para remover o oxigênio por reação com o hidrogênio para formar água), e assim, obter um gás hidrogênio altamente puro.
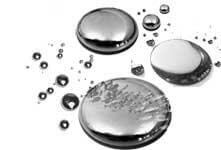
Entre as décadas de 1930 e 1960, várias toneladas de resíduos de mercúrio foram despejadas na Baía de Minamata, no Japão. Milhares de pessoas que viviam ao redor da Baía foram envenenadas por metilmercúrio em virtude do consumo de peixe contaminado. As vítimas sofreram severos danos neurológicos, que mais tarde ficou conhecida como Doença de Minamata. Ao todo, milhares de pessoas foram atingidas e mais de 900 morreram.
Desde então, houve um movimento significativo para substituir a tecnologia de células de mercúrio pelas novas tecnologias tais como: diafragma e de membrana. Atualmente, somente 35% da capacidade mundial (principalmente no oeste e centro da Europa e cerca de 10% da produção dos EUA) de cloro é produzido usando o processo de célula de mercúrio. No Brasil, a capacidade instalada de célula a mercúrio é de 15%. Hoje, em dia não existem mais novas instalações projetadas para a tecnologia baseada em célula a mercúrio.
As instalações existentes no mundo estão tentando diminuir a quantidade de mercúrio perdida durante a fabricação do cloro e da soda cáustica. Sendo que a meta é diminuir a perda para valores menores que as definidas pela Eurochlor (melhor tecnologia conhecida) que é de 1,9 grama/ano/tonelada métrica de cloro produzido. Em 2007 se tornou efetivo o plano da Eurochlor para reduzir as emissões de mercúrio na Europa. Neste plano o objetivo principal era reduzir as emissões para 1,0 g por tonelada de Hg. Os resultados mostram que o nível de emissões caiu de 1,09 g em 2004 para 1,05 g em 2005, sendo que em 2007 o objetivo foi alcançado.
A célula de membrana
A Figura 2.8 mostra uma montagem esquemática de uma célula eletrolítica baseada na tecnologia de membrana polimérica. Como podemos ver, numa célula de membrana, uma membrana que troca íons separa o compartimento anódico do compartimento catódico. A membrana separadora é formada geralmente por uma estrutura em forma de bicamada feita de ácido perfluorocarboxílico ou perfluorossulfônico, formando um sanduiche entre o ânodo e o cátodo. A solução salina saturada é introduzida no compartimento anódico, onde o cloro, por sua vez, é liberado. Então, os íons de sódio migram para o compartimento catódico. Ao contrário das células de diafragma, apenas os íons de sódio e água migram através da membrana. Os íons cloreto, que não sofreram a reação de oxidação no ânodo, e os demais íons inertes presentes em solução permanecem na região anódica sem atravessar a membrana.
Soda cáustica diluída (32%) é introduzida no compartimento catódico, onde os íons de sódio reagem com os íons hidróxido, produzidos durante a reação de formação e desprendimento de gás hidrogênio pela redução das moléculas de água. Assim, a concentração da solução inicial de soda cáustica a 32% fica mais concentrada em virtude da formação de mais moléculas de hidróxido de sódio (soda cáustica), ou seja, concentração da solução de soda cáustica passa a ser de aproximadamente 35%. O gás hidrogênio umidificado sai do compartimento catódico pela parte superior. Uma parte do produto de soda cáustica é retirada do compartimento catódico e vai para o sistema de evaporação e outra parte é diluída para 32% e retorna para o compartimento catódico.
A Tabela 2.3 ilustra a comparação em relação ao consumo de energia e eficiência das diferentes tecnologias usadas para produção de cloro e soda.
Tabela 2.3. Comparação entre as diferentes tecnologias para produção de cloro e soda cáustica.
Diafragma | Membrana | Mercúrio | |
---|---|---|---|
Densidade de corrente de operação (kA/m2) | 0,9 – 2,6 | 3,0 – 5,0 | 8,0 – 13,0 |
Voltagem da célula (Volts) | 2,9 – 3,5 | 3,0 – 3,6 | 3,9 – 4,2 |
NaOH (% m/m) | 12 | 33 – 35 | 50 |
Consumo de energia (kWh/MT* de Cl2)[Densidade de corrente de (kA/m2)] | 2720[1,7] | 2650[5,0] | 3360[10,0] |
Consumo de vapor (kWh/MT* de Cl2) para concentração de 50% NaOH | 610 | 180 | 0 |
Tipos de eletrodos usados
Durante os anos 1900, o ânodo utilizado para a geração de cloro era a platina ou a magnetita. No entanto, por causa do elevado custo da platina e das limitações com respeito a densidade de corrente (0,4 kA/m2) com o uso da magnetita, o grafite se tornou predominantemente o material utilizado como ânodo desde 1913 a meados dos anos 1970. Em 1919, Acheson desenvolveu os ânodos de grafite artificiais, que posteriormente foram modificados por Wheeler, que os impregnou com óleo de linhaça melhorando o seu desempenho eletroquímico.
Entretanto, os eletrodos de grafite apresentavam um grande problema durante longo tempo de operação das células eletrolíticas, ou seja, as placas de grafite sofriam desgastes constantes o que resultava em um aumento da sobretensão da célula, devido ao aumento da distância ânodo-cátodo, o que leva a um aumento do custo de operação. Para sanar o problema, a produção tinha que ser interrompida para que os eletrodos fossem ajustados a uma distância adequada de operação. Isso motivou a busca de eletrodos com estruturas mais resistentes ao desgaste, assim, os ânodos dimensionalmente estáveis, ADE® (do inglês, Dimensionally Stables Anode, DSA®) foram desenvolvidos para substituir os eletrodos de grafite. O metal platina e suas ligas tais como: Pt/Ir ativando titânio apresentava excelente resistência à corrosão em longos períodos de eletrólise com solução de salmoura. No entanto, estes ânodos ainda apresentavam um tempo de vida útil curto e um custo elevado, devido a utilização de platina e irídio (metais nobres).
A história dos eletrodos conhecidos como ânodos dimensionalmente estáveis, se funde com a importância da utilização do RuO2 como material eletroativo que recobre a superfície do eletrodo. Os trabalhos que relatam essa história podem ser verificados numa série de artigos produzidos por Trasatti e Hayfield. A primeira patente dos ADE® apareceu em 1965 e uma segunda em 1967 que foram propostas por Henri Bernard Beer que revolucionaram a indústria de cloro-álcali.
Nestas patentes, Beer descreve o método de preparação dos eletrodos pela técnica de decomposição térmica de precursores de cloretos sobre um substrato de titânio, o qual ficava revestido com os óxidos do grupo da platina ou óxidos metálicos não nobres tais como: TiO2, SnO2, etc. Estes ânodos foram inicialmente usado em células de mercúrio da Denora, e exibiram baixa tensão da célula e uma vida longa.
Consequentemente, ao longo dos anos, a maioria das plantas que utilizavam a tecnologia das células de diafragma em todo o mundo, foram convertidos para estes tipos de eletrodos como ânodo. A Figura 2.9 ilustra alguns tipos de eletrodos utilizados hoje em dia nas diferentes células.
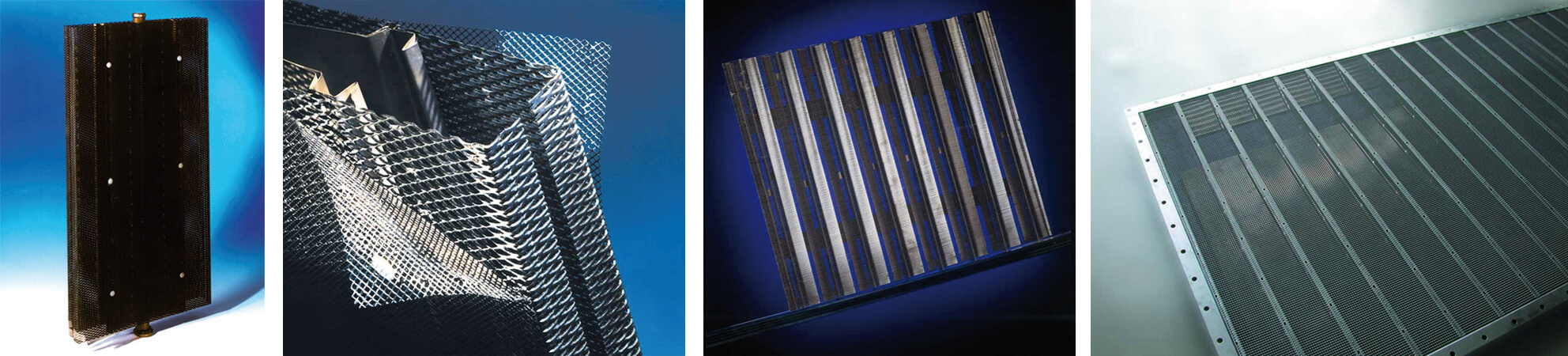
2.3. Teste para garantir a qualidade de produto
Durante a fabricação de Cloro, Soda Cáustica e Hipoclorito de sódio alguns testes são necessários para verificar e garantir a qualidade do produto vendido. Assim, a Associação Brasileira de Normas Técnicas, ABNT, formulou uma série de testes específicos que devem ser realizados para garantir a qualidade do material fabricado. As Tabelas 2.4 e 2.5 apresentam as informações relativas às determinações que devem ser observadas e as respectivas metodologias usadas para tal determinação quando se trabalha com os produtos Cloro, Soda Cáustica e Hipoclorito de sódio.
Tabela 2.4. Determinações e metodologia usadas na verificação da qualidade dos produtos Cloro e Hipoclorito de sódio.
Determinações | Método |
---|---|
Ferro | Espectrofotométrico visível* |
Cloro ativo | Volumétrico |
Teor de clorato | |
Taxa de geração de gases | Gasométrico |
Alcalinidade de hidróxido e carbonato | Potenciométrico/Volumétrico |
Materiais insolúveis | Filtração à vácuo constante |
Tabela 2.5. Determinações e metodologia usadas na verificação da qualidade do produto Soda cáustica.
Determinações | Método |
---|---|
Ferro | Espectrofotométrico visível |
Carbonato | Potenciométrico e Volumétrico* |
Teor de clorato | Volumétrico |
Taxa de sulfato (Na2SO4 < 0,05 % /massa) | |
Alcalinidade total (% NaOH e Na2O) | Espectrofotométrico/Volumétrico |
Mercúrio (0,05 até 10 mg/kg) | Absorção Atômica por Chama |
Sílica (SiO2 < 10 mg/kg) | Espectrofotométrico visível com molibdato de amônio |
Atividade 2.1
Uma das etapas do processo industrial utilizado para a fabricação de cloro e soda cáustica é a eletrólise de uma solução de salmoura (NaCl + H2O). Durante o processo eletrolítico os íons cloretos são convertidos em Cl2 no compartimento anódico e no compartimento cátodo é gerado hidróxido de sódio e gás hidrogênio.
Escreva as equações químicas envolvidas no processo usando células de membranas. Quantos mols de cloro são gerados no ânodo durante a eletrólise da salmoura com uma corrente de 4,00 A por um período de 2 horas?
Dados: Constante de Faraday = 96500 C/mol; 1 A = 1 C/s.
2.4. Construindo e fixando o conhecimento
1. Escreva um resumo contendo no máximo 20 linhas e no mínimo 10 linhas dos três tipos de processos utilizados na produção de cloro e da soda.
2. Explique por que a célula de mercúrio está sendo retirado do mercado, em seguida descreva quais são os problemas relacionados a este tipo de tecnologia.
3. Escreva as reações químicas que ocorrem no ânodo e cátodo durante a fabricação de cloro e soda usando uma célula de diafragma.
4. A Eletroquímica é uma parte da Físico-Química, tendo uma grande importância para o setor Químico Industrial. Um dos processos mais importantes que envolvem a Eletroquímica é a eletrólise de soluções aquosas de NaCl, conhecida como indústria do cloro-álcali. Neste contexto, cite três importantes substâncias produzidas por este processo, em seguida informe quais são os principais setores ou segmentos das indústrias brasileiras que usam essas substâncias.
5. Descreva quais são os materiais que revestem os eletrodos que são colocados no compartimento anódico em uma célula de diafragma? Qual é a função deste material durante a eletrólise da salmoura?
Referências Bibliográficas
SHREVE, R. N., BRINK Jr., J.A. Indústria de Processos Químicos. Vol. Único, trad. 4ª. edição; Guanabara Koogan S.A., Rio de Janeiro, RJ, 1997.
WONGTSCHOWSKI, P. Indústria Química – riscos e oportunidades, 2ª. Edição revista e ampliada; Edgard Blücher LTDA; São Paulo, SP, 2002.
ULLMANN´S. Encyclopedia of industrial chemistry. VCH, New York, NY, 1987.
ABICLOR. Relatório Anual da indústria Brasileira de Álcalis, Cloro e derivados.
http://electrochem.cwru.edu/encycl/art-b01-brine.htm
BOMMARAJU, T. V.; OROSZ, P. J.; SOKOL, E. A. Brine Electrolysis. Process Technology Optimization, Inc. New York, NY, 2007.
TRASATTI, S. Electrocatalysis: Understanding the Success of DSA. Electrochim. Acta 2000, 45, 2377-2385.
TRASATTI, S. Physical Electrochemistry of Ceramic Oxides. Electrochim. Acta 1991, 36, 225-241.
HAYFIELD, P. C. S. Development of the Noble Metal/Oxide Coated Titanium Electrode. Part I: The Beginning of the Story. Platin. Met. Rev. 1998, 42, 27-33.
HAYFIELD, P. C. S. Development of the Noble Metal/Oxide Coated Titanium Electrode. Part II: The Move to Platinum/Iridium to Ruthenium Oxide Electrocatalyst. Platin. Met. Rev. 1998, 42, 46-55.
HAYFIELD, P. C. S. Development of the Noble Metal/Oxide Coated Titanium Electrode. Part III: Coated Titanium Anodes in Widely Ranging Oxygen Evolving Situations. Platin. Met. Rev. 1998, 42, 116-122.
BEER, H. B.British Patent 1,147,442; 1965
BEER, H. B. Electrode for Use in Electrolytic Process. British Patent, 1,195,871, 1967.
ABNT. Associação Brasileira de Normas Técnicas.
O'BRIEN, T. F.; BOMMARAJU, T. V., HINE, F. Handbook of Chlor-Alkali Technology. Springer, New York, NY, 2005.