Capítulo 4 Siderurgia
4.1. Histórico resumido
O ferro foi o, provavelmente, o primeiro metal manipulado pelos homens. Acredita-se que os homens das cavernas usavam o ferro para a fabricação de armas e artefatos agrícolas rudimentar a partir das grandes fogueiras feitas dentro das cavernas usando “pedras” de minério de ferro, que era reduzido pelo calor e o carbono da madeira da fogueira. Já no Egito antigo, a mais de 4.000 anos a.C., o ferro era trabalhado e recebia o nome de “metal celeste”, devido ao fato de ser obtido de meteoritos caídos do espaço. Neste período o ferro era considerado um metal precioso e nobre, semelhante ao ouro nos dias atuais, sendo, portanto usada na manufatura de jóias e adornos. Os esquimós também se valiam da origem meteorítica do ferro para produzir armas de caça, tais como pontas de lança. A expedição de Peary encontrou no Século XX, os restos de um meteorito, com peso aproximado de 40 toneladas, usado por séculos pelo povo esquimó na fabricação de seus artefatos.
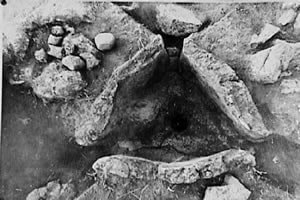
Os fornos mais antigos já encontrados datam do ano 500 a.C. nas Ilhas Britânicas e na Alemanha. Fornos de processos mais evoluídos foram encontrados na Índia e Japão por volta de 500 d. C. A Europa na Idade Média já considerava de extrema importância comercial a produção do ferro. A “forja catalã” era extensivamente utilizada nesta época para a redução direta do minério de ferro que produzia um material duro e quebradiço, usado na produção de armas brancas pesadas de difícil manejo.
Apenas ao redor do ano 1450 se começou a produção de um intermediário denominado ferro gusa, pois era possível se alcançar maiores temperaturas durante o processo. Assim o ferro absorvia maior quantidade de carbono, oriunda do carvão vegetal, que escorri de forma mais fluida, permitindo um manuseio melhor. A posterior oxidação do ferro gusa permitia a obtenção de um aço de melhores propriedades mecânicas, o que permitiu a fabricação de armas brancas mais leves, além de armas de fogo, como os canhões. Data do ano de 1640 o uso do primeiro alto-forno para a produção de ferro gusa. Apesar do grande avanço tecnológico trazido pelo domínio da siderurgia nesta época a necessidade de usar 4 kg de carvão vegetal para a produção de 1 kg de ferro causou uma enorme devastação das florestas. Isto fez a madeira aumentar muito de preço além de provocar restrições legais na exploração da madeira.
Contudo em 1710, na Inglaterra, se passou a usar o coque, que é um derivado do carvão mineral, como substituto ao carvão vegetal. Isto gerou um novo e importante impulso na siderurgia. Porém, foi com a chegada da máquina a vapor, em 1870, que a siderurgia se tornou uma das mais importantes atividades econômicas e industriais dos países civilizados. Este parâmetro é usado até hoje para medir o grau de desenvolvimento de um país.
No Brasil o primeiro grande fato relacionado a siderurgia ocorreu em 1812 com a primeira corrida brasileira de ferro gusa realizada na Vila de Congonhas – MG, atingindo seu auge após a inauguração da Companhia Siderúrgica Nacional (CSN) que continha o único alto-forno do país em Volta Redonda –RJ. Atualmente, o parque siderúrgico brasileiro compõe-se de 27 usinas, administradas por oito grupos empresariais: ArcelorMittal Brasil, Gerdau, CSN, Usiminas, SINOBRAS, V&M do Brasil, Villares Metals e Votorantim Siderurgia.
Atividade 4.1
Faça um breve levantamento histórico sobre a atividade siderúrgica no Estado do Espírito Santo. Não se esquecer de determinar o início das atividades do setor e a conjuntura atual da atividade de siderurgia no Estado.
4.2. Minério de Ferro
O ferro é encontrado na natureza, principalmente, na forma de óxido, embora possa também ser encontrado como carbonatos e sulfetos, em menor ocorrência e até, raramente, na forma nativa. O ferro é o segundo metal mais abundante, perdendo apenas para o alumínio. Os minérios de ferro são:
1) Magnetita: óxido de ferro com fórmula química Fe3O4 (mais especificamente FeO∙Fe2O3), com um teor nominal de ferro de 72,4%, porém com teor real da ordem de 50 a 70%. Esta diferença se deve a presença de ganga no minério. Este tipo de minério apresenta coloração cinza escura a negra, bem como propriedades magnéticas. Esta é uma vantagem tecnológica que torna mais fácil a concentração deste tipo de minério nas etapas de beneficiamento.
Observação: Ganga corresponde a todos os outros minerais encontrados no minério que não tem interesse comercial. Geralmente, a ganga é prejudicial à economicidade da lavra por diminuir o teor, dificultar a extração ou o beneficiamento do minério.
2) Hematita: óxido de ferro com fórmula química Fe2O3, com um teor nominal de 69,5% de ferro, mas um teor real na faixa de 45 a 68%. É o tipo mais comum de minério de ferro e apresenta coloração avermelhada.
3) Limonita: composta, principalmente, de hematita hidrata, com fórmula química Fe2O3∙H2O, podendo conter de 1 a 3 moléculas de hidratação, portanto seu teor nominal de ferro também pode variar. O teor real de ferro encontra-se na faixa de 20 a 50% de ferro e apresenta uma coloração marrom, sendo considerado um minério relativamente pobre em ferro.
4) Siderita: composta por FeCO3 com um teor nominal de 48,3% de ferro e um teor real variando de 10 a 40% de ferro. Minério de baixa ocorrência, normalmente associada com hematita.
5) Pirita: também possui baixa ocorrência e normalmente associada a mistura de minérios de outros metais, como os minérios de cobre. É composta de FeS2 e não apresenta interesse siderúrgico. Devido a sua coloração dourado a pirita foi usada muitas vezes para enganar as pessoas, o que lhe atribui o nome de “ouro dos tolos”.
Os minérios de ferro são normalmente lavrados a céu aberto, devido ao fato de serem basicamente depósitos aluviais. Inicialmente, o minério passa por processos físicos de beneficiamento simples, como fragmentação por britagem, moagem e pulverização, classificação por peneiramento e concentração por métodos de separação magnética. Em seguida, o minério poderá passar por processos químicos de preparação envolvendo aquecimento a altas temperaturas, por exemplo:
1) Calcinação para a desidratação da limonita:
Fe2O3∙H2O → Fe2O3(s) + H2O(g) (T = 800 °C)
equação 4.1E a calcinação da siderita:
FeCO3(s) → FeO(s) + CO2(g) (T = 800 °C)
equação 4.22) Ustulação para a conversão da pirita
4FeS2(s) + 11O2(g) → 2FeCO3(s) + 2SO2(g) (T = 1000 °C)
equação 4.3e oxidação de parte da hematita
2FeCO3(s) + O2(g) → 2Fe3O4(s) (T = 1000 °C)
equação 4.4Então, o minério é aglomerado por processos de sinterização ou pelotização resultando em unidades, com geometria e tamanho apropriados, para ser levado ao alto-forno, além de um teor real de ferro da ordem de 40 a 60%.
4.2.1. Redução do Minério no alto-forno
A redução do minério, na forma de óxido, utilizando o carbono, proveniente do coque, é realizada em um forno específico para esta atividade chamado alto-forno. O alto-forno é um reator tubular vertical onde a redução ocorre de forma contínua, sendo alimentado com carga sólida na parte superior que entra em contato com o ar pré-aquecido na parte inferior, conforme mostrado na Figura 4.2. No Estado do Espírito Santo a antiga Companhia Siderúrgica do Tubarão (CST), atual Arcelor Mittal, opera com este tipo de processo para a redução do ferro.
A carga de um alto-forno é composta principalmente por minério de ferro, coque e fundente. O minério de ferro é, normalmente, composto por hematita ou uma mistura de hematita e magnetita, contendo cerca de 40 a 60% de ferro. Este minério costuma conter cerca de 10% de ganga, cujo componente principal é a sílica (SiO2). O coque, obtido da destilação prévia da hulha ou de outro carvão mineral, é o fornecedor de carbono, para as reações de redução do ferro, além de desempenhar a função de combustível. Já o fundente, tem a função de baixar o ponto de fusão da escória e, geralmente, é composto por calcário (CaCO3) que é calcinado no interior do alto-forno formando cal (CaO).
A reação de redução do minério de ferro pelo coque é uma reação endotérmica, ΔH > 0, enquanto que a reação de combustão de parte do coque com o oxigênio do ar (insuflado de 800 a 1.000 °C) é exotérmica, ΔH < 0. Os produtos finais das reações dentro do alto-forno podem ser classificados em quatro categorias: ferro gusa, escória, poeira e gases. O ferro gusa é o ferro no estado líquido com um teor de 3 a 4% de carbono e 6 a 7% de impurezas e outros elementos, os mais comuns são: enxofre, fósforo, silício e manganês provenientes da ganga ou do coque. As primeiras etapas de redução do ferro geram um material sólido e esponjoso que se funde ao chegar a zonas de temperaturas mais elevadas. O ferro no estado líquido se deposita no fundo do alto-forno, de onde é recolhido a cada corrida. A escória é uma mistura de óxidos fundidos de densidade menor que o ferro gusa, seus componentes provém do fundente e da ganga do minério, sendo retirada, geralmente, antes da corrida do ferro gusa. A poeira é constituída basicamente de cinzas que resultam da queima do coque e de materiais inertes da ganga, saindo na parte superior do alto-forno por carreamento dos gases produzidos. Os gases saem na parte superior do alto-forno a 300 °C. Os principais componentes são CO2 e CO, sendo a proporção de CO/CO2 da ordem de 2 a 3. Estes gases são, normalmente, aproveitados no pré-aquecimento do ar a ser insuflado no alto-forno.
4.2.2. Reações no alto-forno
A redução do minério de ferro em um alto-forno ocorre durante a queda da carga sólida, ou seja, ao redor de 10 segundos. A redução é realizada por uma série de reações de acordo com a zona do forno (temperatura) alcançada.
A zona de redução indireta está localizada na parte superior do alto-forno e possui temperaturas na faixa de 100 a 700 °C. Nesta zona, praticamente toda a hematita é reduzida a magnetita, conforme reação química apresentada na equação 4.5:
6Fe2O3(s) + C(s) → 4Fe3O4(s) + CO2(g) (T = 500 °C)
equação 4.5com ΔH = +15 kcal mol−1 e ΔG = −27 kcal mol−1.
A zona de redução direta está situada a cerca de meia altura do alto-forno e possui temperaturas da ordem de 700 a 1.500 °C. Nesta zona, a magnetita é reduzida a ferro metálico esponjoso, conforme a reação química apresentada na equação 4.6:
Fe3O4(s) + 4C(s) → 3Fe(s) + 4CO(g) (T = 1000 °C)
equação 4.6com ΔH = +250 kcal mol−1 e ΔG = −50 kcal mol−1.
A zona de fusão e combustão está localizada na parte inferior do alto-forno, imediatamente acima do banho de escória e ferro gusa, e trabalha com temperaturas variando de 1.500 a 1800 °C. É nesta zona que ocorre a fusão do ferro esponjoso formado na zona anterior e a combustão do coque que ainda não reagiu, conforme as reações químicas mostradas nas equações 4.7 e 4.8:
Fe(s) → Fe(l) (T = 1530 °C)
equação 4.7com ΔH = +3,5 kcal mol−1.
2C(s) + O2(g) → 2CO(g) (T = 1800 °C)
equação 4.8com ΔH = +56 kcal mol−1 e ΔG = −150 kcal mol−1.
A redução direta da segunda etapa é uma síntese de redução intermediária da magnetita (Fe3O4) a wustita (FeO) que posteriormente é reduzida ao ferro, conforme as reações químicas mostradas nas equações 4.9 e 4.10:
Fe3O4(s) + C(s) → 3FeO(s) + CO(g) (T = 1000 °C)
equação 4.9com ΔH = +145 kcal mol−1 e ΔG = −17 kcal mol−1.
3FeO(s) + 3C(s) → 3Fe(s) + 3CO(g) (T = 1000 °C)
equação 4.10com ΔH = +105 kcal.mol−1 e ΔG = −33 kcal.mol−1.
A soma das etapas (eq. 4.9 e eq. 4.10), de acordo com a lei de Hess, permite obter os produtos representados na eq. 4.6.
Um segundo mecanismo que poderá acontecer na zona de redução direta corresponde a formação de CO2 intermediário, conforme as reações químicas mostradas nas equações 4.11, 4.12 e 4.13:
2Fe3O4(s) + C(s) → 6FeO(s) + CO2(g) (T = 1000 °C)
equação 4.116FeO(s) + 3C(s) → 6Fe(s) + 3CO2(g) (T = 1000 °C)
equação 4.124CO2(g) + 4C(s) → 8CO(g) (T = 1000 °C)
equação 4.13A soma das três equações anteriores, segundo a lei de Hess, também produzirá a reação química mostrada na equação 4.6. De forma idêntica, a reação química mostrada na equação 4.8 pode ser desdobrada nas reações químicas representadas pelas equações 4.14 e 4.15:
C(s) + O2(g) → CO2(g) (T = 1800 °C)
equação 4.14CO2(g) + C(s) → 2CO(g) (T = 1800 °C)
equação 4.15Uma terceira hipótese de mecanismo de redução na zona de redução direta é a que considera o CO como agente redutor e não o carbono do coque, conforme as reações químicas representadas pelas equações 4.16 e 4.13:
Fe3O4(s) + 4CO(g) → 3Fe(s) + 4CO2(g) (T = 1000 °C)
equação 4.164CO2(g) + 4C(s) → 8CO(g) (T = 1000 °C)
equação 4.13Novamente, a soma destas duas equações, de acordo com a lei de Hess, deverá produzir a reação química mostrada na equação 4.6.
Todas estas reações mostradas até agora são classificadas como as reações principais de um alto-forno. Porém, reações secundárias também podem ocorrer. Dentre as reações secundárias merecem destaque a calcinação do fundente, representadas por meio das equações 4.15, 4.17 e 4.18, e a redução paralela dos óxidos de silício e manganês da ganga, mostradas por meio das equações 4.19 e 4.20, respectivamente:
CO2(g) + C(s) → 2CO(g) (T = 1800 °C)
equação 4.15CaCO3(s) → CaO(s) + CO2(g) (T = 1000 °C)
equação 4.17Cuja a soma, segundo a lei de Hess, fornece:
CaCO3(s) + C(s) → CaO(s) + 2CO(g) (T = 1000 °C)
equação 4.18com ΔH = +80 kcal mol−1 e ΔG = −220 kcal mol−1.
SiO2(s) + 2C(s) → Si(l) + CO(g) (T = 1800 °C)
equação 4.19com ΔH = +150 kcal mol−1 e ΔG = −15 kcal mol−1.
MnO(s) + C(s) → Mn(l) + CO(g) (T = 1800 °C)
equação 4.20com ΔH = + 65 kcal mol−1 e ΔG = −10 kcal mol−1.
O silício e o manganês produzidos conforme apresentados por meio das equações 4.19 e 4.20 são incorporados ao ferro gusa.
4.3. Redução do minério usando outros processos
Sem dúvida a redução utilizando um alto-forno é o principal processo de produção de ferro, contudo muitas vezes este tipo de instalação é inviável, pois requer grandes áreas e enormes investimentos. Buscando-se alternativas surgiram os chamados processos diretos, alguns produzindo ferro gusa e outros produzindo ferro sólido denominado ferro esponja. Porém, estes processos correspondem apenas a uma parcela pequena da produção de ferro e aço. Os principais processos não-convencionais para a redução de minério de ferro são apresentados a seguir.
4.3.1. Redução em forno elétrico
Normalmente empregado em países que dispõem de energia elétrica barata e/ou com o coque caro ou inexistente. As unidades operacionais deste tipo de processo são pequenas, na ordem de 100 a 200 t/dia. Neste processo não há consumo de coque como combustível, mas uma fonte de carbono deve ser empregada como agente redutor. Além da redução no consumo de coque outra vantagem deste processo é que não há a necessidade de injeção de ar no sistema, uma vez que não há combustão. Como desvantagem cita-se o alto consumo de energia elétrica, da ordem de 2.000 kW/t de ferro. As reações químicas envolvidas no processo de redução utilizando forno elétrico são as mesmas observadas para processos utilizando alto-fornos, excetuando-se a reação de combustão do coque.
4.3.2. Processo Wiberg-Södefors
Este processo foi desenvolvido em 1918 na cidade de Södefors na Suécia por Martin Wiberg. Ele se baseia na redução direta do minério de ferro para obtenção do ferro esponja, o que permite que as temperaturas envolvidas no processo sejam da ordem de 1.000 °C, bem menores que as temperaturas máximas atingidas no alto-forno (1.800 °C). Neste processo são usados dois agentes redutores: o gás hidrogênio (H2) e o monóxido de carbono (CO), na proporção de 1:2, respectivamente. Os gases redutores são formados em uma torre adjacente chamada carburator que é aquecida eletricamente usando dois eletrodos de grafita. O carburator é alimentado por coque com alto teor de enxofre (baixa qualidade) que reage com vapor de água a 1.100 °C para produzir os gases redutores conforme apresentado por meio da equação 4.21:
C(s) + H2O(g) → H2(g) + CO(g) (T = 1000 °C)
equação 4.21com ΔH = + 35 kcal mol−1 e ΔG= −15 kcal mol−1.
Os gases redutores produzidos são conduzidos a uma coluna de dolomita queimada, para retirada do enxofre que estava contido no coque. Este enxofre reage com o hidrogênio formado pela Equação 4.21 formando ácido sulfídrico, H2S, que reage com o cálcio da dolomita formando CaS. Após a retirada de enxofre a mistura redutora é encaminhada para o forno de redução onde reage com o minério em sistema contracorrente, como ocorre no alto-forno, à mistura entra pela parte inferior do forno e a carga pela parte superior. A redução ocorre conforme as reações químicas ilustradas pelas equações 4.22 e 4.23, na parte superior do forno:
Fe2O3(s) + CO(g) → 2FeO(s) + CO(g) (T = 900 °C)
equação 4.22Fe2O3(s) + H2(g) → 2FeO(s) + H2O(g) (T = 900 °C)
equação 4.23Já na parte inferior do forno a redução ocorre conforme as reações químicas ilustradas pelas equações 4.24 e 4.25:
FeO(s) + CO(g) → Fe(s) + CO2(g) (T = 1000 °C)
equação 4.24FeO(s) + H2(g) → Fe(s) + H2O(g) (T = 1000 °C)
equação 4.25Neste tipo de processo as unidades operacionais têm capacidade média de 300 t/dia.
4.3.3. Processo HyL (Hojalata y Lámina)
Este processo também usa mistura redutora de H2 e CO, porém em uma proporção maior de H2 (H2/CO ~ 5). O processo HyL foi desenvolvido em 1953 pela Companía Hojalata y Lámina, localizada na cidade de Monterrey no México. É um processo viável principalmente para países que possuam grande disponibilidade de metano barato, bem como de minério de ferro. A mistura redutora é produzida pela reação do metano com o vapor de água, usando níquel como catalisador, conforme mostrado na Equação 4.26:
O processo de redução ocorre em fornos tipo retortas, de forma intermitente, para a geração de ferro esponja, com unidades operacionais de 500 t/dia de capacidade. A grande vantagem deste processo é dispensar o uso de coque e a principal desvantagem é ser intermitente.
4.3.4. Processo Ferro-H (ferro hidrogênio)
Neste processo somente o H2 é usado como agente redutor do minério de ferro e utiliza um sistema de leito fluidizado, no qual o minério em pó é mantido em suspensão por uma corrente ascendente de gases. Portanto, o minério deve ser beneficiado até a obtenção de um pó bem fino. O H2 é produzido pela reação do metano com o vapor de água, mostrada na Equação 4.26, e o CO formado na reação é separado, fazendo-se o gás produzido atravessar uma mistura de monoetanolamina e, em seguida, por uma solução de acetato de cobre e amônia à 50 atm de pressão. O H2 puro é então inserido no forno de redução promovendo as seguintes reações químicas:
3Fe2O3(s) + H2(g) → 2Fe3O4(s) + H2O(g) (T = 600 °C, P = 30 atm)
equação 4.27Fe3O4(s) + 4H2(g) → 3Fe(s) + 4H2O(g) (T = 600 °C, P = 30 atm)
equação 4.28As unidades de produção deste processo costumam ser pequenas e caras, com capacidade da ordem de 10 t/dia.
Atividade 4.2
Compare de forma sucinta e dissertativa a redução indireta (processo usando o alto-forno) e os processos de redução direta do Ferro. Não se esquecer de destacar as principais diferenças e similaridades existentes entre os processos.
4.4. Produção de aço
Os aços são soluções sólidas intersticiais de carbono no ferro, com o teor de carbono variando de 0,02 a 2%. Muitas vezes os aços são referidos como ligas ferro – carbono, contendo como impurezas o enxofre e o fósforo em teores abaixo de 0,05%. Os aços isentos de elementos de liga adicionados de forma intencional são chamados aço ao carbono e os que contêm elementos adicionados de forma intencional, tais como, níquel, cromo, molibdênio, entre outros, são ditos aço-liga. Os aços ao carbono são muito mais baratos e fáceis de produzir que os aços-liga. As propriedades do aço, e consequentemente suas aplicações, são altamente dependentes do teor de carbono presentes no aço. Aços com teores de carbono abaixo de 0,2% são chamados de aços doces. Além disso, elementos de liga também podem alterar de forma muito significativa às propriedades do aço. A produção do aço a partir do ferro gusa ocorre pela redução de diversos elementos, conforme dados apresentados na Tabela 4.1.
Tabela 4.1. Faixas típicas de composição química (em peso) de ferro gusa e aço doce.
Elementos | Ferro Gusa (%) | Aço Doce (%) |
---|---|---|
Carbono | 3 - 4 | 0,02 - 0,1 |
Silício | 1 - 3 | 0,02 - 0,1 |
Manganês | 0,5 - 1,5 | 0 - 0,02 |
Enxofre | 0,01 - 0,2 | 0,01 - 0,1 |
Fósforo | 0,05 - 2 | 0,05 - 2 |
A redução dos teores destes elementos é necessária para melhorar as propriedades do ferro gusa, pois estes elementos formam compostos intermetálicos com o ferro, que comprometem a aplicação do ferro gusa. O enxofre, por exemplo, causa fragilidade a quente devido a formação de sulfeto de ferro, FeS, que se funde nas etapas de conformação mecânica, como o forjamento, segregando e causando trincas e até a ruptura do material. Já o fósforo causa fragilidade a frio devido a formação do fosfeto de ferro, Fe3P, que possui elevada dureza. O carbono pode formar um carbeto com o ferro que recebe o nome de cementita (Fe3C), que também possui dureza muito elevada e causa fragilidade no material. A diminuição dos teores destes elementos, melhorando as propriedades do material, é alcançada pela passagem do oxigênio, puro ou do ar, através do ferro gusa fundido, em temperaturas da ordem de 1.600 °C, promovendo a oxidação destes elementos. Estas reações de oxidação são exotérmicas, permitindo a manutenção da temperatura sem combustão paralela.
Atividade 4.3
Escreva as reações de oxidação dos elementos apresentados na Tabela 4.1.
A oxidação do ferro gusa normalmente é conduzida pela insuflação de ar em fornos chamados de conversores Bessemer. Estes fornos tem capacidade de 50 toneladas de aço e podem ser ácidos ou básicos, dependendo do tipo de escória gerada e do tipo de refratário utilizado. Os conversores ácidos são empregados para a redução de ferro gusa contendo teores extremamente baixos de fósforo. Neste caso o tipo de escória formada é ácida e os tijolos refratários que devem ser utilizados também são ácidos, a base de sílica (SiO2). Já o ferro gusa contendo elevado teor de fósforo, usa um conversor com tijolos refratários básicos, a base de dolomita ou magnesita, pois escória básica é formada pela adição de cal (CaO) como fundente, para a retirada do fósforo. O tempo de oxidação, também chamado de período de sopragem, é de 15 minutos. A quantidade de sucata que pode ser empregada neste processo é de apenas 10% da carga final.
O sopro de ar no lugar de oxigênio puro pode levar a elevados valores de nitrogênio no aço, podendo formar nitretos, o que prejudicaria o desempenho do produto final. A oxidação usando oxigênio puro levará mais tempo, porém permitira o aumento da carga de sucata para 20%. Os principais processos de oxidação em conversores que usam oxigênio puro, com capacidade variando de 50 a 100 toneladas são comentados a seguir:
1) Processo LD: semelhante ao conversor Bessemer exceto pelo fato do forno não apresentar caixa inferior de sopragem. A sopragem é feito através de uma lança, tudo oco, introduzido pela boca do forno. Esse processo foi desenvolvido na Áustria no ínicio do século XX e seu nome, LD, refere-se às duas fábricas que primeiro o usaram, Linz e Donawitz. No Estado do Espírito Santo a antiga Companhia Siderúrgica do Tubarão (CST), atual Arcelor Mittal, opera com este tipo de processo em sua aciaria.
2) Processo Kaldo: derivação do processo LD, com rotação do forno, o que permite melhor homogeneização do banho de ferro gusa que se oxida a aço. Este processo foi desenvolvido na Suécia pelo Prof. Kalling na cidade de Domnarfvert, que uniu a primeira sílaba de seu nome com a primeira sílaba da cidade para dar o nome ao processo, KALDO.
3) Processo Rotor: o mais eficiente dos processos usando oxigênio puro e deriva do processo Kaldo, com um forno giratório e duas lanças para soprar o oxigênio. Esta disposição permite carregar o forno com até 30% de sucata.
4) Processo Spray: baseia-se na oxidação gota-a-gota do ferro gusa e por isso apresenta altíssima eficiência, porém o custo do aço produzido por este processo é extremamente elevado.
A necessidade cada vez maior de se reciclar grandes quantidades de sucata faz o processo Siemens-Martin ser ainda muito utilizada, pois ele permite o uso de até 60% da carga de sucata. Porém faz-se necessária a queima de combustível para se fundir a carga. De modo a aumentar a eficiência térmica do processo, o forno Siemens-Martin possui um sistema de regeneração de calor operando de forma alternada. Este processo foi desenvolvido em meados do Século XX, por Siemens na Alemanha e por Martin na França de forma simultânea. A capacidade do processo é da ordem de 500 a 600 toneladas e seu tempo de operação varia de 8 a 16 horas.
A fabricação de aço de maior qualidade pode ser conduzida usando um forno a arco elétrico. Este tipo de forno pode operar com carga composta apenas de sucata, contudo, grandes quantidades de energia elétrica são necessárias. A fusão da carga se dá pela formação do arco elétrico entre três eletrodos de grafite pirolítico e a carga sólida. A capacidade deste tipo de forno é da ordem de 10 a 50 toneladas e seu tempo de operação varia de 1 a 2 horas.
4.5. Construindo e fixando o conhecimento
1. Quais são os principais tipos de minério de ferro e quais são os teores de ferro presentes em cada um deles?
2. Qual é a diferença entre os processos de calcinação e ustulação? Escreva as equações químicas relativas a estes processos.
3. Como é composta a carga do alto-forno?
4. Qual é o rejeito do alto-forno? De que é composto?
5. Como são divididas as zonas de um alto-forno? Quais são as principais reações que ocorrem em cada zona?
6. Quais são os produtos oriundos do processo de redução de minério de ferro?
7. Quais são os requisitos para a utilização de fornos elétricos de redução de minério?
8. Quais são as principais diferenças entre o aço e o ferro gusa?
9. Qual impureza causa fragilidade a frio no aço? E qual causa fragilidade a quente? Por que estes fenômenos acontecem?
10. Explique em que situação deve-se empregar tijolos refratários ácidos e básicos em um conversor.
Referências Bibliográficas
CAMPOS FILHO, M. P. Introdução a Metalurgia Extrativa e Siderurgia. 1ª Edição, Ed. LTC / FUNCAMP, Campinas, SP, 1981, 153p.
CANTO, E. L. Minerais, Minérios, Metais, De onde vêm? Para onde vão? 2ª Edição, Ed. Moderna, São Paulo, SP, 2010, 143p.